The Project
Impressions from the project process
Project Information
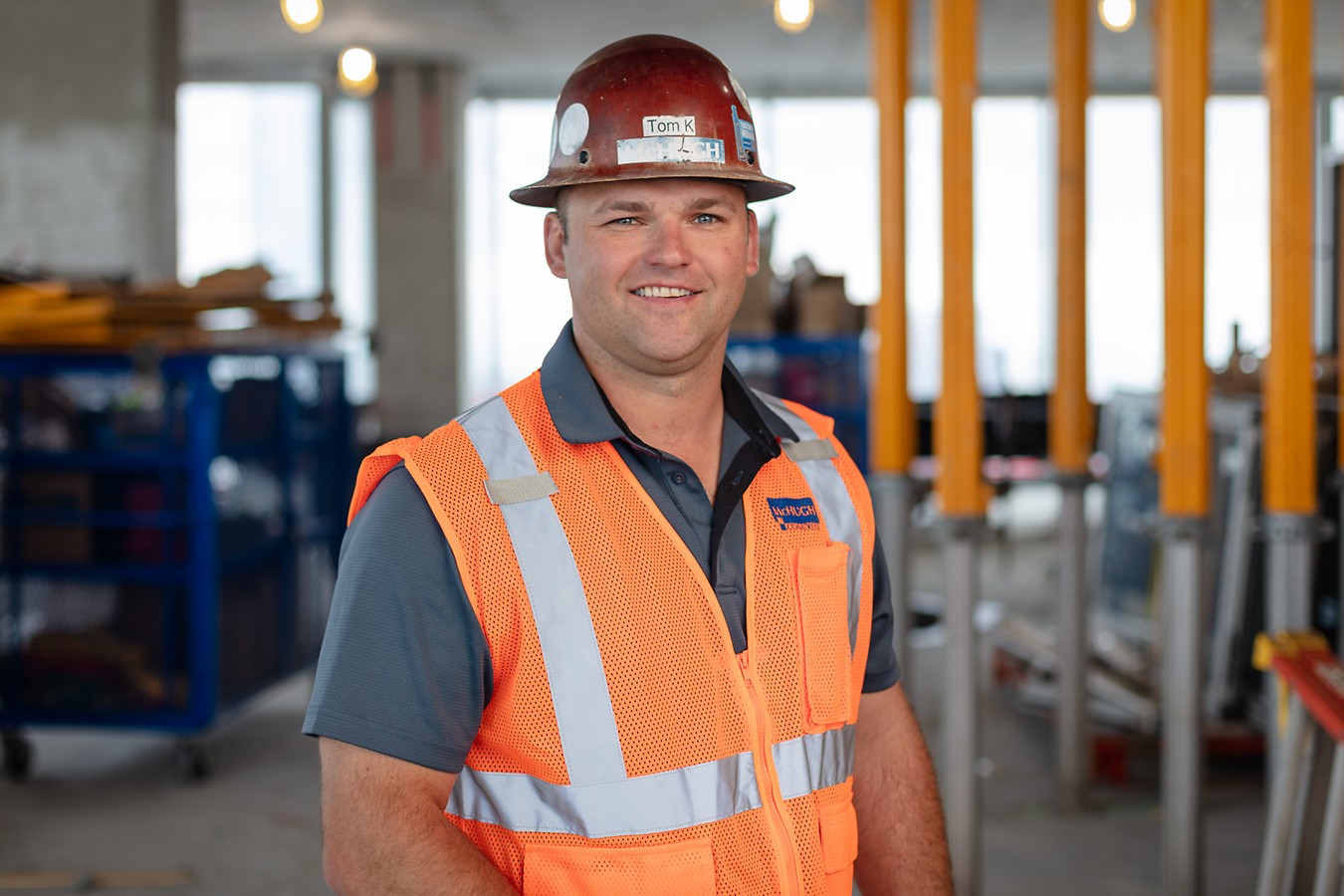
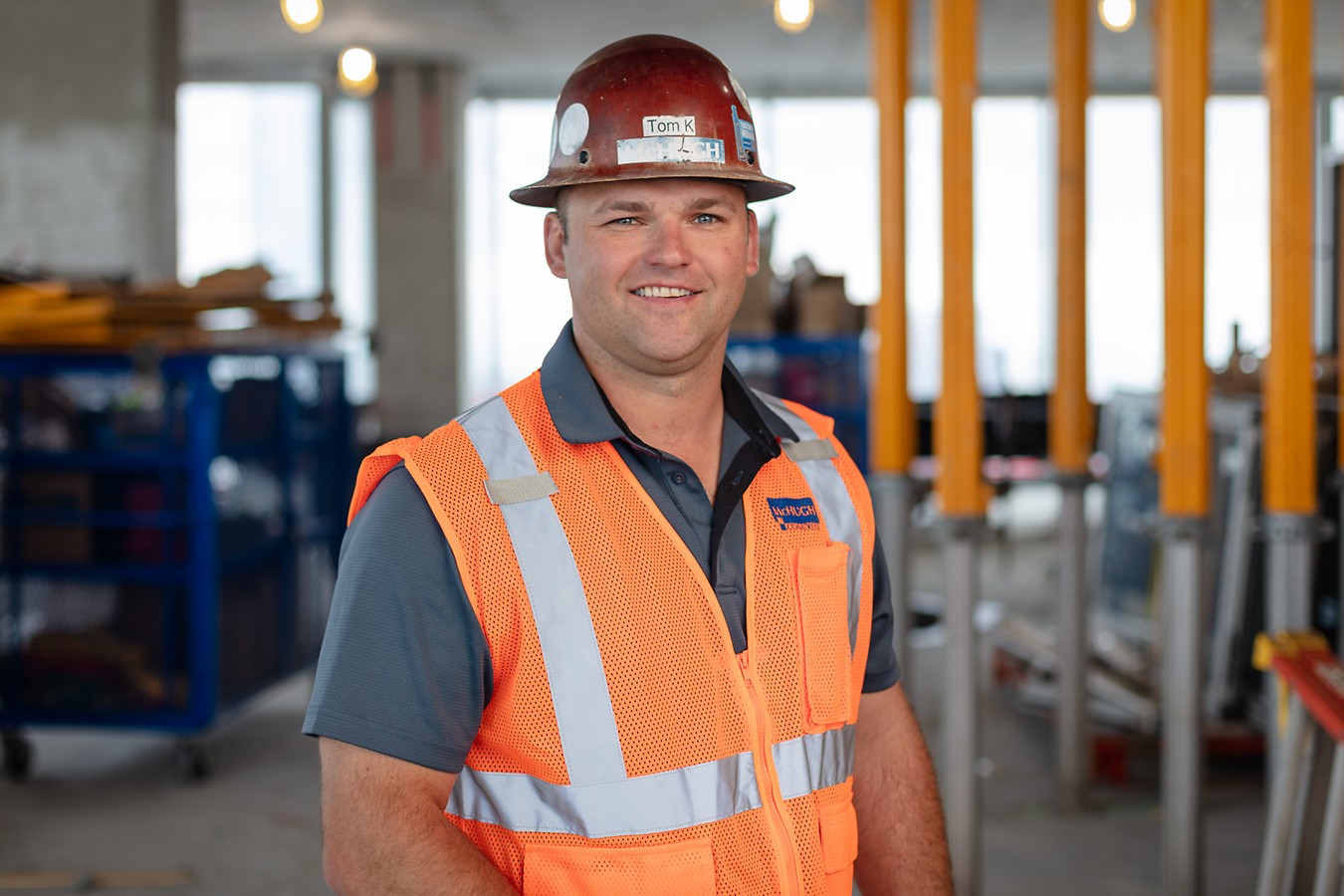
Tom Kruszewski
Superintendent
The project had an aggressive schedule requiring all 4 phases of the project to be constructed simultaneously, which required several unique formwork solutions. The construction sequence required a complicated core formwork solution that started in a forty-foot-deep earth retention system, various crane-lifted walls, and a complete perimeter of windscreens on both towers. McHugh Construction selected PERI Formwork Systems to supply and engineer the formwork that was instrumental in completing the project efficiently and ahead of schedule.
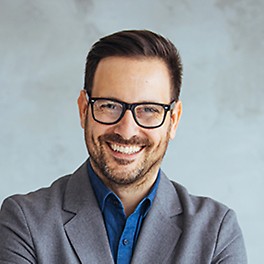
Call us on +1 410-712-7225 to discuss your requirements further.
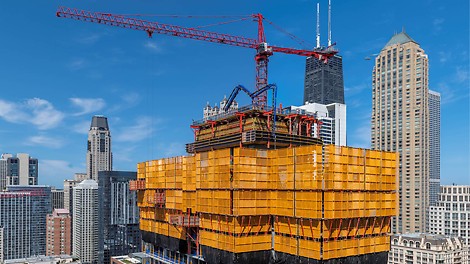
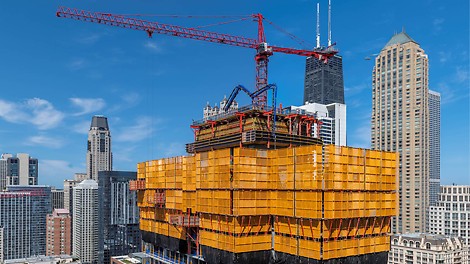