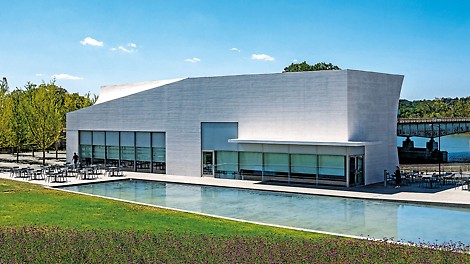
The REACH at Kennedy Center
Washington D.C., United States
In a city of monuments, appearance is important. So, when plans began to come together for the first major expansion of the John F. Kennedy Center for the Performing Arts in Washington, D.C., white architectural concrete was a natural choice.
Architects who dream big continually challenge those who are charged with bringing their dreams to fruition. Such was the case on this project, where the concrete contractor, The Lane Construction Corporation, began working with PERI Formwork Systems very early in the process to develop the detailed project strategy that would be required.
Coming nearly half a century after the construction of the original facility, the expansion project took advantage of the advancements in concrete construction —specifically self-consolidating concrete and 3-D modeling - which made this project buildable, but still far from easy.
Known as the REACH, the expansion consists of three new buildings strategically placed on the 4.6-acre site extending along the Potomac River south of the existing structure. The new structures feature both crisp, clean lines and sweeping curves that complement, rather than replicate, the hewn Carrara marble columns of Edward Durell Stone’s original design and provide a variety of flexible indoor and outdoor spaces.
Numerous facilities were constructed below grade to provide additional parking space, multipurpose rehearsal studios, and classrooms, but the project’s predominant features are three plaza-level structures above grade. All are white cast-in-place concrete with various architectural finishes including multiple board form patterns.
Contractor
Lane Construction
The Project
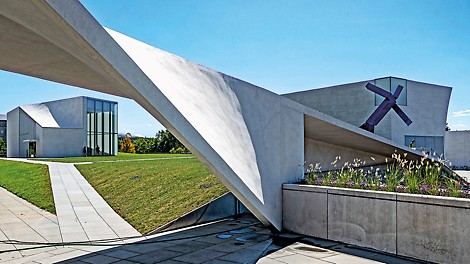
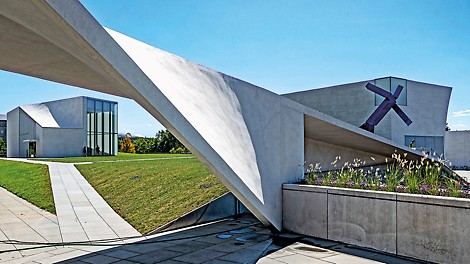
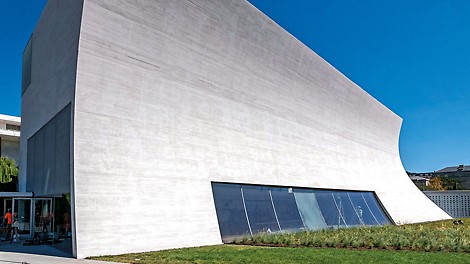
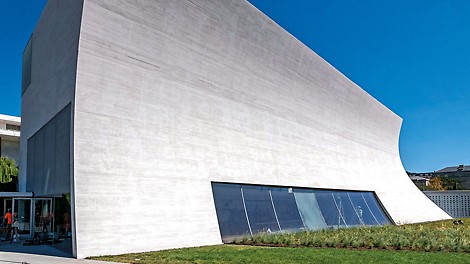
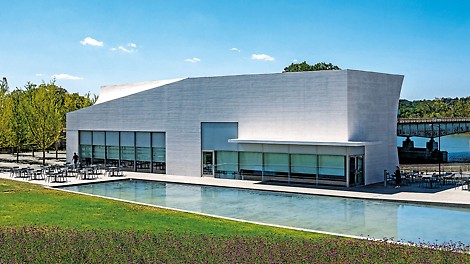
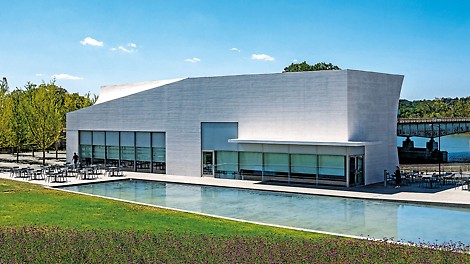
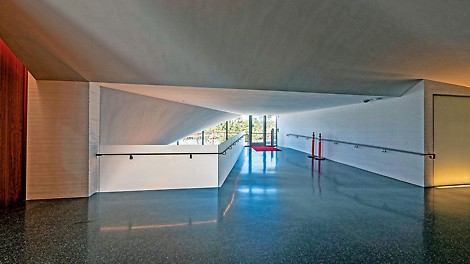
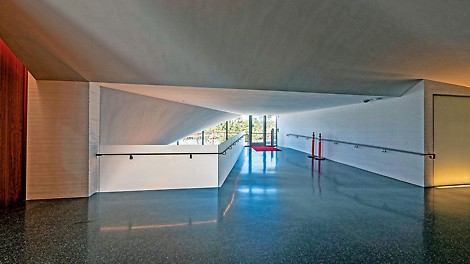
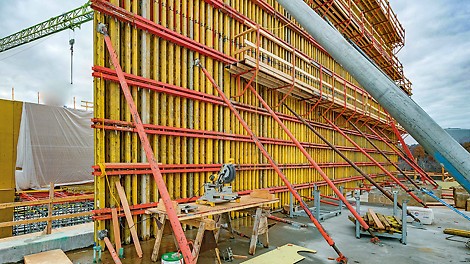
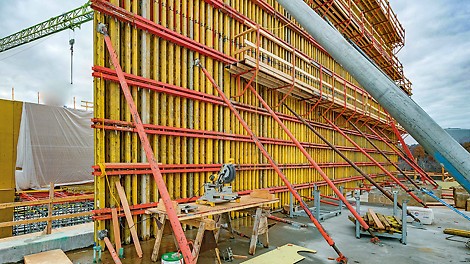
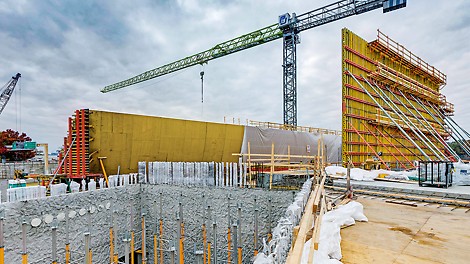
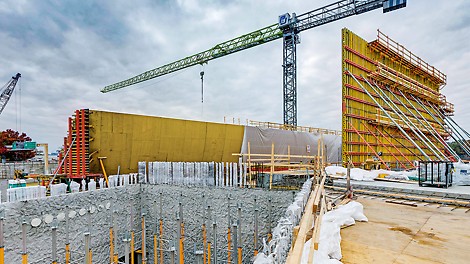
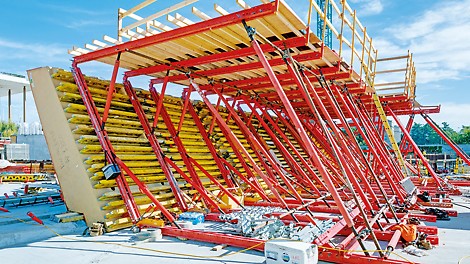
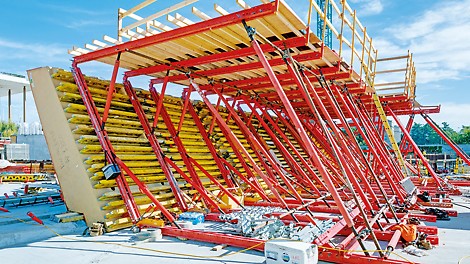
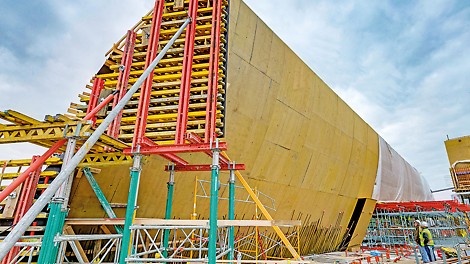
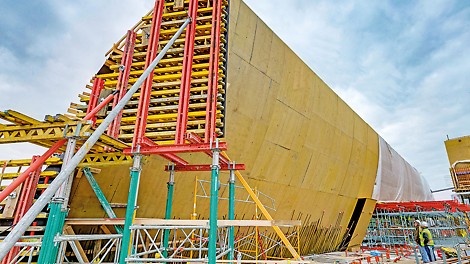
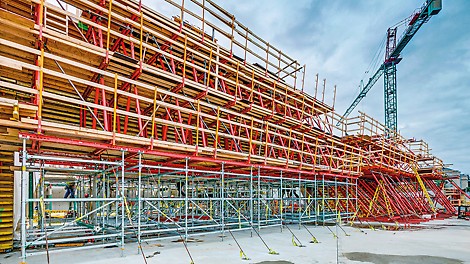
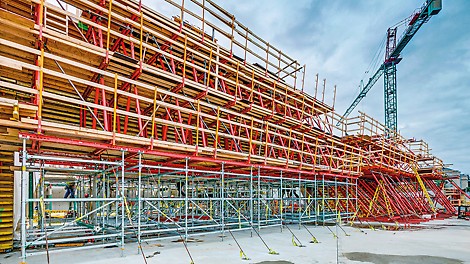
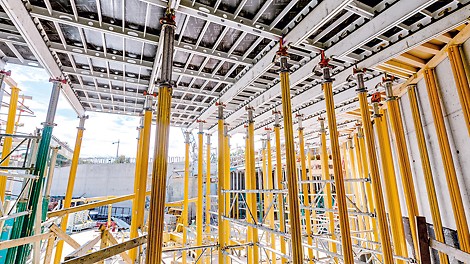
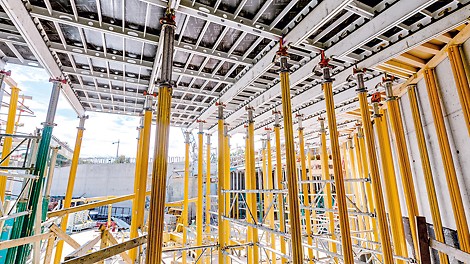
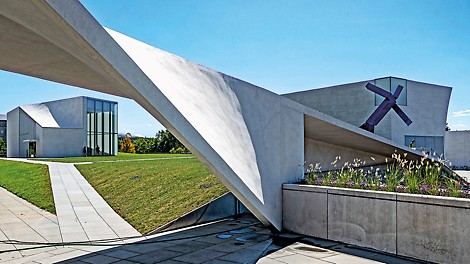
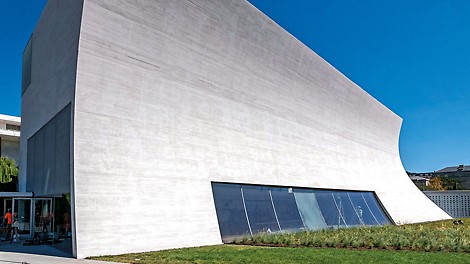
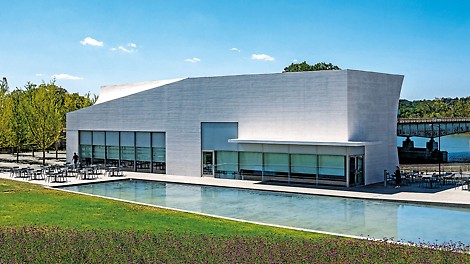
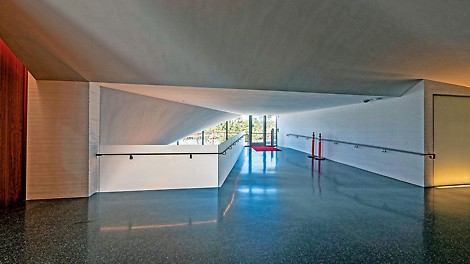
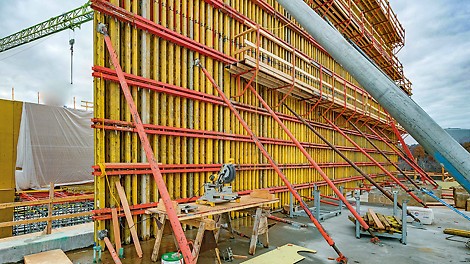
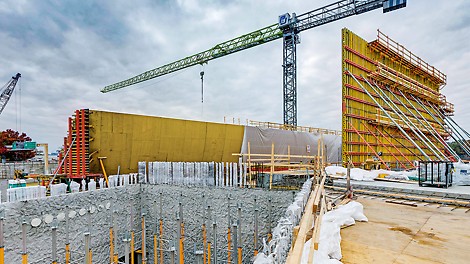
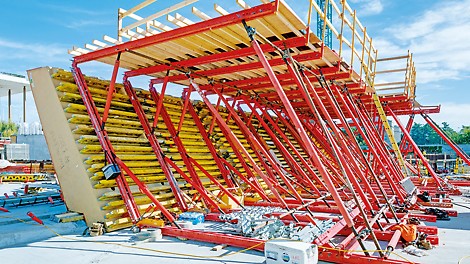
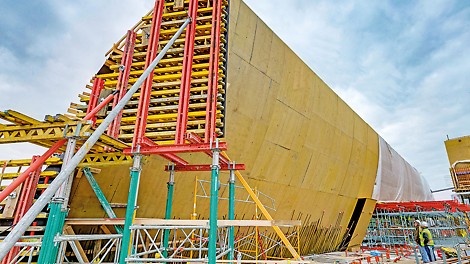
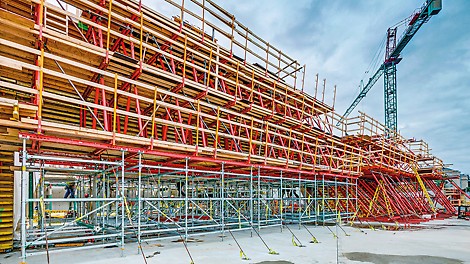
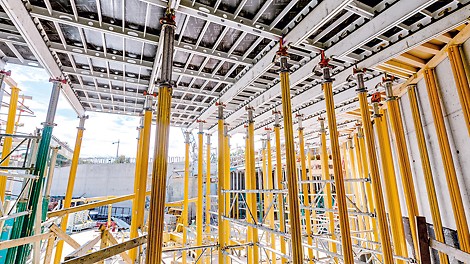
Project Information
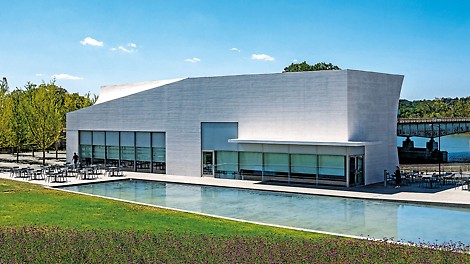
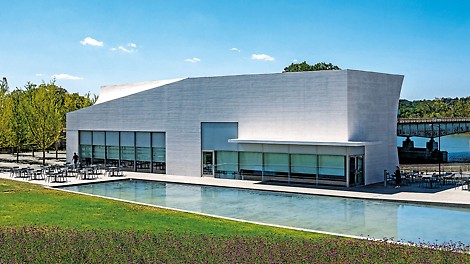